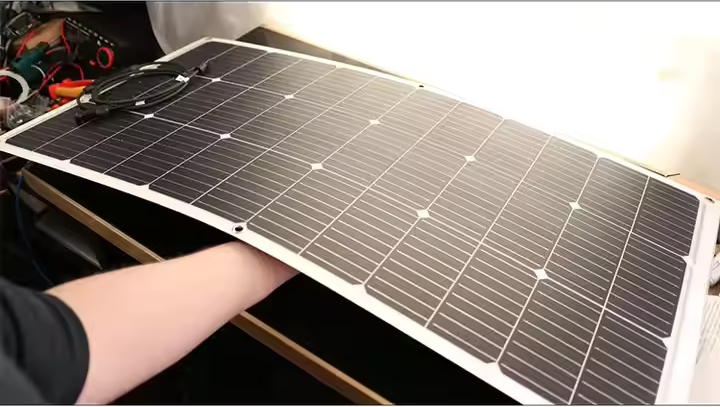
Solar panels play a pivotal role in transforming sunlight into renewable energy, making them an essential component of sustainable living. But have you ever stopped to wonder how these brilliant devices are made? From raw materials like silicon to the final assembly, the process involves advanced technology, precision, and a focus on quality assurance.
Whether you’re a renewable energy enthusiast or an eco-conscious consumer curious about the origins of solar panels, this guide will break down the manufacturing process step by step. By the end of this blog, you’ll have a deeper appreciation for the intricate craftsmanship and technology behind every solar panel.
Understanding Solar Panels
Before we explore how solar panels are made, it’s vital to understand their primary components and functions. Solar panels are made up of several critical parts:
- Photovoltaic Cells: These are the main components that absorb sunlight and convert it into electricity. They are typically made from silicon, a semiconducting material.
- Metal Frame: Usually made of aluminum, this provides structural integrity and protects the panel.
- Glass and Protective Layers: A front glass layer shields the solar cells from environmental elements, while a plastic backsheet adds further protection.
- Wiring: Metal conductors are arranged in a grid pattern to efficiently collect and transfer electricity generated by the cells.
Key to their efficiency is the arrangement of the cells and the quality of the materials used. Now, let’s move on to the fascinating process of how these components come together.
The Solar Panel Manufacturing Process
Solar panel production is a meticulous process involving multiple stages. These steps ensure that every solar panel meets high-performance and durability standards. Here’s how it works:
1. Extracting Silicon from Sand
It all begins with silicon. Quartz minerals, found in sand, are the raw materials used to produce silicon for solar cells.
- Purification Process: Silicon is heated to 1,410°C to remove impurities in an energy-intensive process involving coal as a reducing agent.
- Outcome: The purified silicon is then collected in solid rock form as the foundation for creating photovoltaic cells.
2. Creating Silicon Ingots
Once purified, the silicon is further processed to form ingots:
- Melting Silicon: The silicon rocks are melted at high temperatures in a cylindrical furnace.
- Crystallization: This process produces monocrystalline (single-crystal) or polycrystalline (multiple-crystal) ingots. Monocrystalline silicon offers higher efficiency, while polycrystalline is a more cost-effective option.
3. Slicing Silicon Wafers
The silicon ingots are then sliced into thin layers called wafers.
- Diamond-Coated Wire Saws: These tools create precise, thin slices of silicon.
- Anti-Reflective Coating: To improve efficiency by reducing sunlight reflection, a specialized coating is applied to the wafers.
This step generates a byproduct known as kerf, or silicon sawdust, which is often recycled to minimize waste.
4. Assembling Solar Cells
Next comes the assembly of solar cells:
- Creating P-N Junctions: The wafers are treated with materials like phosphorus and boron to form p-n junctions. This is critical for generating a flow of electricity.
- Metallic Grid Connections: Thin lines of metal are added to form a grid, allowing the flow of electrons to be collected efficiently.
These solar cells form the building blocks of a functional solar panel.
5. Constructing Solar Panels
Once the cells are assembled, they are integrated into solar panels:
- Connecting Solar Cells: Typically, 60 or 72 solar cells are soldered together using metallic connectors.
- Encapsulation: Layers of ethylene vinyl acetate (EVA) are added to bind the cells and protect them from wear and tear.
- Adding the Glass Layer: A durable glass, usually 6-7 mm thick, forms the front protective layer.
- Metal Frame: Aluminum frames are attached to provide stability and protect against environmental damage.
6. Installing Junction Boxes
A junction box is installed to consolidate wiring connections, allowing solar panels to integrate seamlessly into electrical systems. This component ensures proper functionality in residential and commercial setups.
7. Testing and Quality Assurance
Rigorous testing is conducted throughout the manufacturing process to ensure solar panels meet high standards of durability and efficiency:
- Durability Testing: Panels are tested to withstand impact, extreme temperatures, and harsh weather conditions.
- Electrical Output Measurements: Parameters such as voltage and power output are evaluated.
- Final Inspections: Any defective panels are discarded, while quality panels undergo final testing before being cleaned and packaged for shipping.
Types of Solar Panels
There are three main types of solar panels, each with distinct characteristics:
- Monocrystalline Solar Panels
- Made from single silicon crystals.
- Known for their high efficiency and sleek black appearance.
- Polycrystalline Solar Panels
- Made from multiple silicon crystals, giving them a distinct blue, shattered-glass look.
- More affordable but slightly less efficient than monocrystalline panels.
- Thin-Film Solar Panels
- Flexible and lightweight, they are ideal for unconventional surfaces and portable setups.
- Commonly made from cadmium telluride (CdTe) or amorphous silicon.
Environmental Impact of Solar Panel Manufacturing
Although solar panels are a clean energy solution, their production comes with environmental challenges:
- Energy-Intensive Production: Manufacturing silicon wafers and ingots requires significant energy and emits carbon dioxide. However, emissions are lower compared to fossil fuel-based energy sources.
- Recycling and Waste Management: Around 90% of decommissioned solar panels end up in landfills in the U.S., highlighting the need for improved recycling efforts.
- Sustainable Practices: Manufacturers are increasingly adopting eco-friendly methods to minimize their carbon footprint, such as using renewable energy in production facilities.
Where Are Solar Panels Made?
Solar panel production is a global effort:
- China dominates the market, manufacturing around 80% of the world’s solar panels.
- Other major players include the U.S., Germany, Malaysia, and Vietnam.
Leading manufacturers include Jinko Solar, LONGi, and First Solar, among others.
Why Quality Matters
The expected service life of solar panels ranges from 20 to 40 years. This emphasizes the importance of thorough quality checks during production. Investing in reliable, high-performance solar panels ensures long-term energy production and savings.
Final Thoughts on Solar Panel Manufacturing
The creation of solar panels involves a fascinating blend of advanced engineering, precise craftsmanship, and rigorous quality control. From extracting silicon to assembling the final product, every step in the process is vital for ensuring the efficiency and durability of these renewable energy powerhouses.
If you’re considering investing in solar panels, understanding their manufacturing process can help you make an informed decision. Look for high-quality panels with certifications to guarantee efficiency and reliability for years to come.
Feeling inspired to go solar? Begin your renewable energy journey with the right solar panels for your home or business.