This series describes the process of designing and building a sustainable home, which is passing tests for airtightness and proved to retain heat in winter. But the Xcel stumbling block has yet to be overcome.
Throughout the design and build of my home, there have been multiple ways that I’ve described my home – sustainable, Passivhaus-inspired, green build, etc. But at its core, my home is high performance. That means it delivers superior energy efficiency, exceptional comfort, healthy indoor air quality, and a reduced environmental footprint. These aren’t just buzzwords, but measurable key performance indicators (KPIs) that can be tested for design validation.
One of the foundational elements for an energy efficient home is its airtightness, which is measured using a blower door test. The test provides air leakage information related to the volume of the home, and it is measured in air changes per hour (ACH). This metric shows how often the entire volume of indoor air is replaced by outside air in an hour through unwanted leaks. In cold climates like Minnesota, uncontrolled air leakage means heat loss, higher utility bills and less comfort in the winter. The opposite is true in hot climates. In Minnesota, the state building code allows up to 3.0 ACH, which means the entire home’s air volume could be replaced three times per hour. No wonder the furnace is constantly running in typical new builds!
Throughout construction, Paltrin, a Minnesota green home builder, had the ACH assessed as critical energy-efficiency measures were implemented. After installing 15 inches of insulation around the building envelope and over 24 inches in the attic, Paltrin performed the first blower door test, achieving an ACH of 0.8, which was a significant improvement over code minimum at a point in the middle of the build process. Even at this stage, there was already tangible results.
“Instead of hauling in massive propane heaters which are typically needed for winter builds, we kept the shell warm all winter with two 1.5 kW space heaters. During a −10 °F stretch, a crew member unknowingly unplugged them, not realizing they were the primary heat source. Remarkably, the home maintained its temperature through the next day—not only underscoring the effectiveness of the design, but demonstrating how smart design can also reduce the carbon footprint of the build process” said Justin Riddle, president of Paltrin.
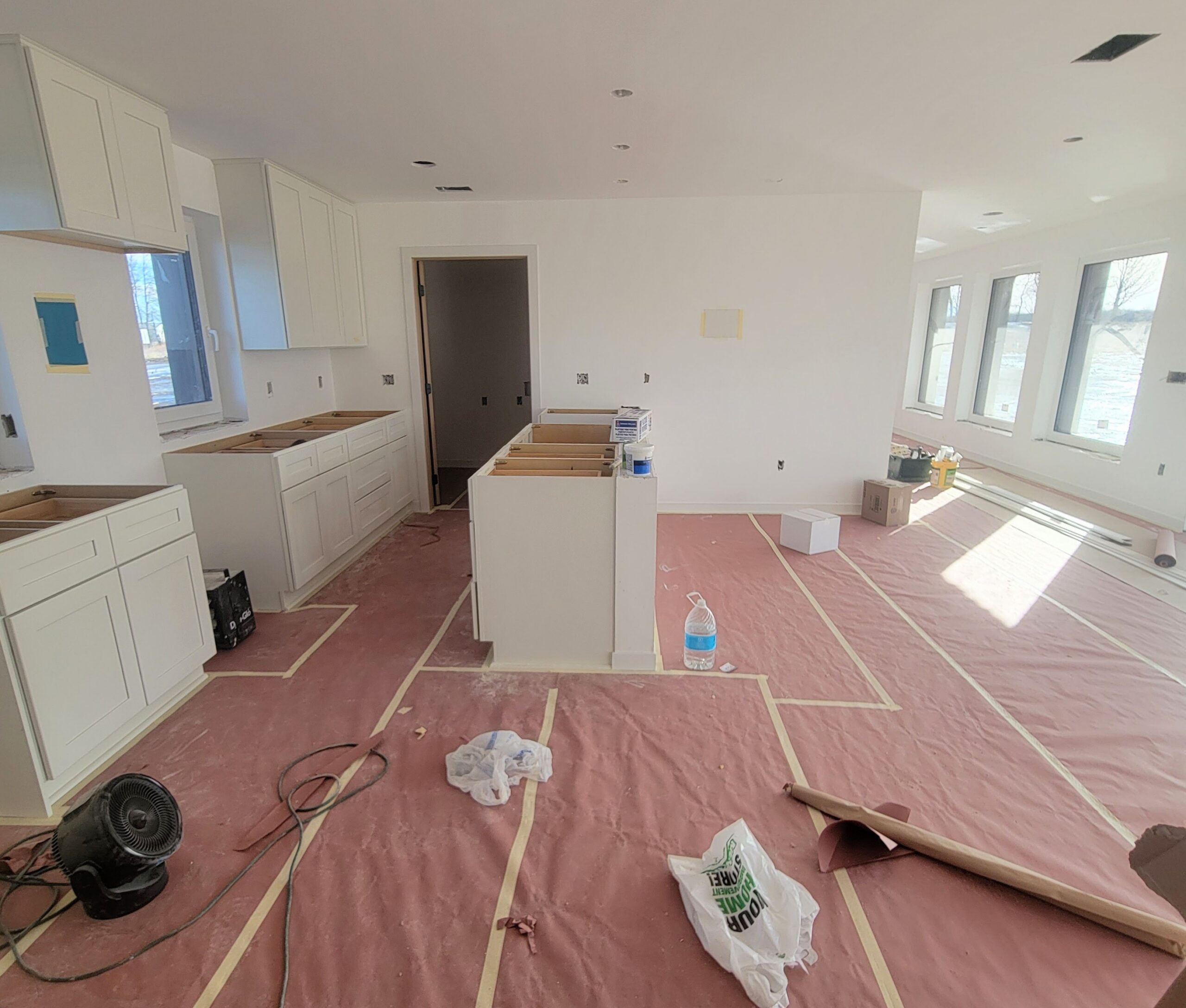
Image: Paltrin
To push airtightness even further, Paltrin applied an advanced aerosol-based air sealing technology to the home and the ductwork. This method distributes a non-toxic sealant throughout the building envelope using positive pressure, targeting and sealing microleaks in hard-to-reach places. The second blower door test showed an impressive 0.34 ACH, meaning it would take about 3 hours for the air inside to be replaced, or about 90% better than code.
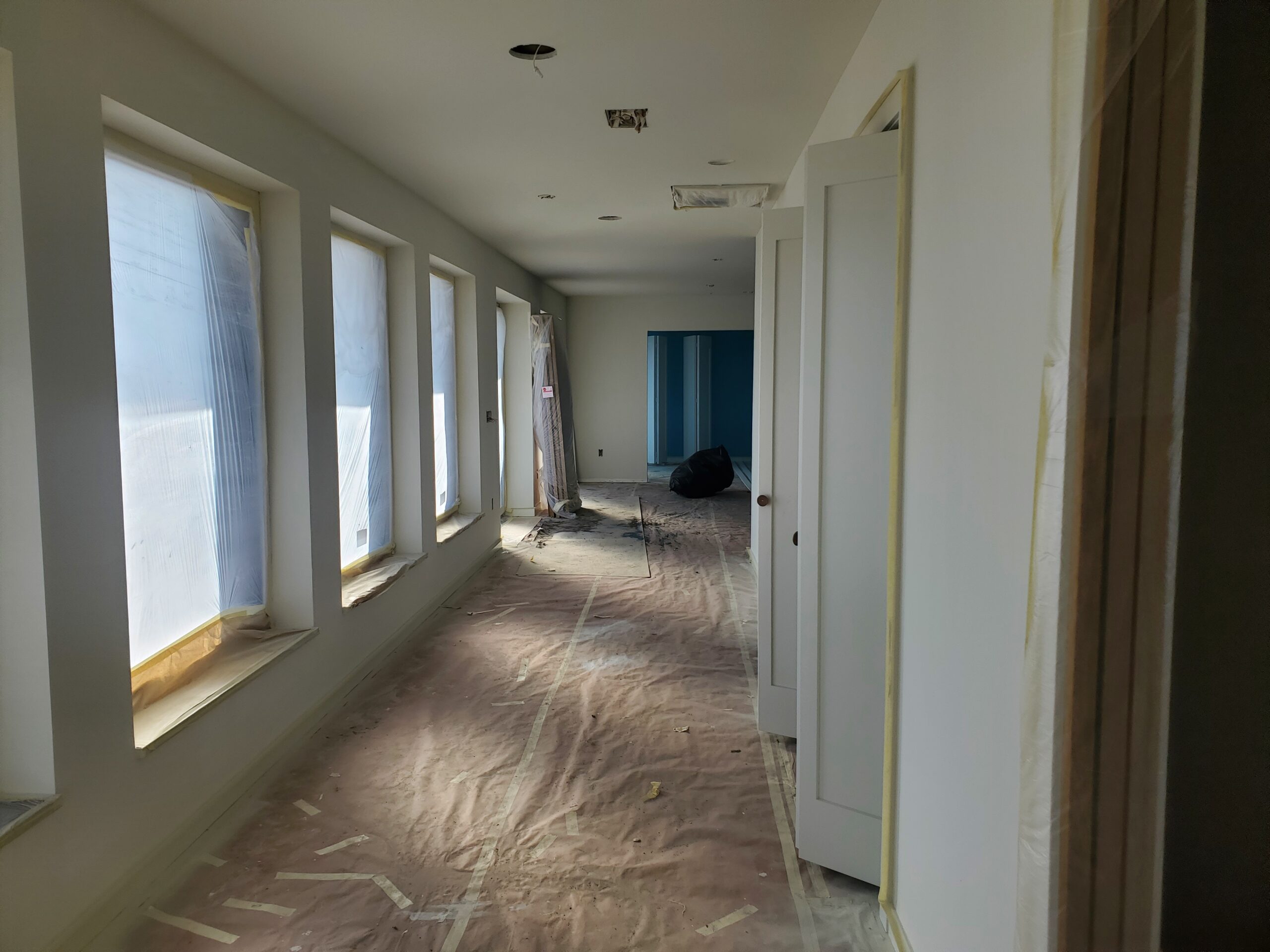
At such a low ACH, natural and uncontrolled air infiltration is nearly eliminated meaning that controlled, mechanical ventilation is essential for indoor air quality. To meet this need efficiently, Paltrin installed an energy recovery ventilator (ERV). It transfers up to 85% of heat from outgoing stale air to incoming fresh air, maintaining temperature and humidity balance while reducing internal pollutants and ensuring constant airflow of fresh filtered air from outdoors to the living space.
Another key element of improving energy efficiency is mitigating thermal bridges. Thermal bridging occurs when heat passes through conductive materials like metal fasteners, wood framing or window and door components creating unwanted paths for heat transfer and undermining overall efficiency. Often invisible without an infrared camera, these bridges can significantly decrease comfort and increase energy use. For my home, one of the examples where we eliminated thermal bridging was at the junction where the concrete slab meets the foundation wall. We mitigated the thermal bridge by installing a continuous layer of insulation between the exterior foundation wall and the interior slab. Because concrete is a strong thermal conductor, this detail was critical to improving the home’s overall energy performance.
One final energy-related design element was integration of passive solar into the home by installing large south‑facing windows, specified with a higher solar heat gain coefficient (SHGC) to maximize beneficial winter solar gain. Sunlight entering these windows is absorbed as heat by the exposed concrete slab, which acts as thermal mass for storing the energy during the day and releasing it gradually to maintain stable indoor temperatures at night. To prevent summertime overheating, a larger overhang was designed above the southern glazing to shade the windows when the sun is high, while still allowing low‑angle winter sun to pass beneath it and warm the interior. This combination of high‑SHGC glazing, thermal‑mass concrete, correctly sized overhangs, and mitigation of thermal bridging will ensure year‑round comfort with minimal active heating or cooling.
While all of these are critical for the house to achieve high performance and minimize the site energy consumption, I am still working to get a PV system installed as part of the goal of reducing the environmental impact of the home.
Xcel denied my application due to a claimed oversupply at the feeder level, so I am moving forward with a supplemental review. I’ll provide more detail about this process in a subsequent article, but I am currently in a race against time with the U.S. Congress potentially overturning the investment tax credit and Minnesota congress considering a bill to significantly weaken net metering, while Xcel is allotted plenty of time for the additional reviews.
Jessica Fishman, director of renewable energy at Kiterocket, is a strategic marketing leader with nearly 20 years’ experience, including seven years as head of global public and media relations at inverter maker SolarEdge. Passionate about addressing climate change by accelerating the clean energy transition, she has worked at leading renewables companies, building marketing and communications departments.
Read the first in the series of Building not your average dream home.
The views and opinions expressed in this article are the author’s own, and do not necessarily reflect those held by pv magazine.
This content is protected by copyright and may not be reused. If you want to cooperate with us and would like to reuse some of our content, please contact: editors@pv-magazine.com.